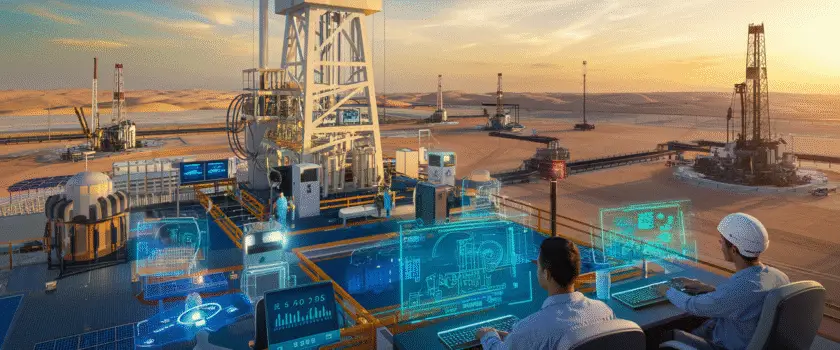
How Oil, Water and Gas Wells function in the Middle East Oil industry using the latest technology
Ever wondered how engineers extract every last drop of oil from beneath scorching desert sands? Spoiler: it’s not just about drilling a hole and watching it flow.
The Middle East oil industry has evolved dramatically, with extraction technology that would make sci-fi writers jealous. Advanced oil, water and gas wells now operate like underground surgical instruments, precisely navigating complex reservoirs with real-time data feedback.
For field engineers and operations managers, understanding these technological marvels isn’t just interesting—it’s essential for maximizing production while minimizing environmental impact.
And that billion-dollar question keeping executives awake at night? How to balance cutting-edge innovation with the harsh realities of desert operations where a single equipment failure can cost millions?
What most industry veterans don’t tell you is that the real game-changer isn’t what happens at the wellhead. It’s what happens next…
Overview of Middle East Oil Industry
A. Current production capacity and global significance
The Middle East sits on roughly 48% of the world’s proven oil reserves. That’s not just impressive—it’s game-changing for the global energy landscape. Saudi Arabia alone pumps out about 10 million barrels per day when operating at full capacity, while the UAE, Kuwait, Iraq, and Iran collectively contribute another 15+ million barrels daily.
This region doesn’t just produce oil—it essentially controls the global oil market’s pulse. When OPEC+ (dominated by Middle Eastern producers) decides to cut or increase production, the entire world feels it at the gas pump within weeks.
B. Major oil-producing countries and key players
Saudi Aramco dominates the scene as the world’s most valuable company, controlling Saudi Arabia’s vast reserves. But the landscape includes other heavyweights too:
Country | Key Players | Approximate Daily Production |
---|---|---|
Saudi Arabia | Saudi Aramco | 10 million barrels |
UAE | ADNOC | 3 million barrels |
Kuwait | Kuwait Petroleum Corporation | 2.7 million barrels |
Iraq | Basra Oil Company, others | 4.5 million barrels |
Iran | National Iranian Oil Company | 2.5 million barrels |
These national oil companies wield enormous power, though they increasingly partner with international players like ExxonMobil, Shell, and BP for technological expertise.
C. Economic impact and future projections
Oil revenues make up over 40% of GDP for countries like Saudi Arabia and Kuwait. The numbers are staggering—Saudi Arabia alone generates roughly $500 million in oil revenue daily during normal market conditions.
The region faces a fascinating crossroads. While actively diversifying economies through initiatives like Saudi Vision 2030 and the UAE’s post-oil strategy, they’re simultaneously investing billions to maximize remaining oil assets.
Industry projections suggest Middle Eastern oil will remain crucial through at least 2050, though its share may gradually decline as renewable energy gains traction.
D. Unique geological challenges in Middle Eastern reservoirs
Middle Eastern oil fields present distinctive challenges. Many are aging giants—like Saudi’s Ghawar field, producing since the 1950s—requiring advanced recovery techniques to maintain output.
The region’s carbonate reservoirs differ significantly from sandstone formations found elsewhere, demanding specialized extraction approaches. Extreme desert conditions with temperatures regularly exceeding 50°C (122°F) strain equipment and infrastructure.
Water scarcity creates another hurdle, as many enhanced oil recovery techniques require substantial water injection. This has pushed regional operators to pioneer seawater treatment facilities and alternative recovery methods that minimize freshwater usage.
Modern Well Drilling Technologies
Advanced directional and horizontal drilling techniques
Gone are the days of simple vertical wells. Middle Eastern oil companies now deploy advanced directional and horizontal drilling that’s revolutionizing access to previously unreachable reservoirs.
These techniques let operators drill at precise angles, extending reach up to 12 kilometers horizontally from a single pad. This means fewer surface facilities and minimal environmental impact—critical in sensitive desert ecosystems.
The game-changer? Rotary steerable systems that give drillers real-time control of the wellbore direction without stopping operations. They’re hitting pay zones with millimeter-level precision, boosting recovery rates by up to 300% compared to conventional wells.
Real-time drilling monitoring systems
The drilling floor’s transformed into something like mission control. Engineers now monitor every aspect of downhole conditions instantly through LWD (Logging While Drilling) and MWD (Measurement While Drilling) systems.
These tools transmit critical data—temperature, pressure, formation characteristics—to surface teams before the drill bit even moves another inch. Problems that once took days to detect now trigger alarms in seconds.
In UAE and Saudi fields, fiber optic sensing cables run alongside wellbores, creating what operators call “smart wells” that continuously monitor production conditions across their entire length.
Automated drilling rigs and robotics
Walk onto a modern Middle Eastern drilling platform and you’ll notice something strange—fewer people. That’s because automation has taken over the dangerous, repetitive tasks.
Iron roughnecks now handle pipe connections without human intervention. Automated pipe handling systems move heavy tubulars with precision that human crews can’t match. Some rigs in Qatar and Kuwait operate with crews half the size needed just ten years ago.
The newest systems integrate AI to “learn” from past drilling data, automatically adjusting parameters to maximize rate of penetration while minimizing risks.
High-temperature resistant equipment innovations
Middle East reservoirs present extreme challenges with temperatures frequently exceeding 175°C. Standard equipment simply fails in these conditions.
The industry’s response? Revolutionary materials science. New elastomer compounds maintain seal integrity at temperatures that would destroy conventional rubber. Advanced ceramic components replace metal parts in critical applications.
Electronic systems now feature specialized cooling systems and temperature-resistant circuitry that continue functioning where previous generations would fail within hours.
These innovations aren’t just technical victories—they’re economic game-changers that have opened up ultra-deep reservoirs previously considered undrillable.
Intelligent drill bits and downhole optimization
Today’s drill bits barely resemble their predecessors. They’re packed with sensors and adjustable cutting structures that adapt to changing formation conditions automatically.
PDC (Polycrystalline Diamond Compact) bits with variable blade profiles can transition between hard and soft formations without tripping out of hole. Some cutting-edge bits even incorporate micro-hydraulics that adjust fluid flow patterns based on real-time drilling conditions.
In Oman’s complex carbonate reservoirs, these smart bits have slashed drilling time by 40% while extending bit life threefold.
The industry’s pushing boundaries with bits that can sense and respond to formation changes without surface intervention—creating wells that practically drill themselves.
Oil Well Engineering Breakthroughs
Enhanced oil recovery methods specific to Middle East formations
The Middle East’s unique geology demands specialized recovery approaches. Gone are the days of simple extraction – now it’s about squeezing every drop from challenging formations.
Water flooding dominates the region, with Saudi Aramco pioneering sophisticated injection patterns tailored to their massive carbonate reservoirs. They’re achieving recovery rates up to 70% in some fields – numbers that were fantasy just decades ago.
CO2 injection is gaining serious traction too. Abu Dhabi’s ADNOC has invested billions in capturing carbon from industrial sources and pumping it underground. Smart move – it boosts recovery while reducing emissions.
Chemical EOR is the next frontier. Kuwait Oil Company’s polymer flooding experiments are showing 15-20% production increases in mature fields where conventional methods hit their limits.
Smart completion systems for maximum productivity
Smart wells are revolutionizing Middle Eastern production. These aren’t your grandfather’s wells.
Intelligent completions with downhole flow control valves allow operators to manage multiple zones from a single wellbore. Qatar’s North Field now features completions with up to 8 independently controlled zones per well.
Real-time monitoring through fiber optic sensing has become standard in Saudi Arabia’s newest developments. Operators can see temperature and pressure changes along the entire wellbore, spotting problems before they become disasters.
The game-changer? Autonomous inflow control devices that automatically adjust based on fluid properties. When water or gas breakthrough occurs, these devices restrict flow without human intervention.
Artificial lift technologies for aging wells
As Middle East fields mature, artificial lift systems have evolved dramatically.
Electric submersible pumps (ESPs) dominate the landscape, but with crucial modifications for the region’s harsh conditions. The latest ESPs handle temperatures up to 400°F and can operate in highly deviated wellbores.
Gas lift remains popular, especially in Kuwait and Iran, where new digitally controlled gas lift valves optimize injection rates continuously. These smart systems have extended the economic life of fields by decades.
Progressive cavity pumps are making surprising inroads in heavy oil operations in Oman, where their ability to handle viscous crudes and sand production outweighs maintenance challenges.
Cutting-edge production optimization software
Digital transformation is the newest revolution in Middle East oil fields.
Predictive analytics platforms like those deployed by PDO in Oman now forecast equipment failures days before they happen. Their maintenance costs have dropped 30% since implementation.
Digital twins are changing the game in Saudi Arabia, where Aramco has created virtual replicas of entire field operations. Engineers simulate changes before implementing them in the real world.
AI-powered production optimization algorithms continuously adjust thousands of variables across giant fields. UAE operators report 5-8% production increases just from better software – that’s millions of barrels annually without drilling a single new well.
Water Well Management in Arid Conditions
Groundwater detection using satellite and drone technology
The Middle East oil industry has revolutionized water management with cutting-edge detection methods. Satellite imaging now identifies potential groundwater reservoirs by analyzing terrain, vegetation patterns, and thermal signatures that indicate water presence. These systems can map aquifers hundreds of meters below the surface.
Drones equipped with ground-penetrating radar (GPR) take this a step further. They fly over vast desert areas collecting high-resolution data about subsurface conditions in hours instead of weeks. One Saudi project mapped 15,000 square kilometers in just 10 days—work that would’ve taken months with traditional methods.
The real game-changer? Machine learning algorithms that process this massive data, highlighting promising water sources with 85% accuracy rates. Operators can now pinpoint drilling locations with unprecedented precision.
Sustainable water extraction methods
Gone are the days of haphazard pumping that depleted aquifers. Smart well systems now monitor extraction rates in real-time, automatically adjusting pumping to maintain sustainable yields.
Horizontal drilling techniques, borrowed from oil extraction, allow operators to access water with minimal surface disturbance. A single horizontal well can replace 3-5 conventional wells, dramatically reducing environmental impact.
Pulse extraction methods—where pumping alternates with rest periods—have shown to increase aquifer longevity by 30% in UAE field tests. These systems use AI to optimize the pulse-rest cycle based on continuous monitoring data.
Variable frequency drives (VFDs) on pumps adjust energy use to water demand, saving up to 40% on power consumption while preventing aquifer damage from over-pumping.
Advanced filtration and treatment systems
Water treatment in Middle Eastern oil operations has made quantum leaps. Nanofiltration membranes now remove contaminants at the molecular level, turning brackish water into usable resources.
Electrocoagulation systems—using electricity instead of chemicals to remove impurities—reduce treatment costs by 25% while eliminating hazardous chemical handling. These systems fit on mobile platforms that can be deployed directly to well sites.
Forward osmosis technology uses significantly less energy than traditional reverse osmosis, perfect for remote operations with limited power infrastructure. Kuwait’s largest oil field reduced water treatment energy consumption by 35% after implementing this technology.
UV-LED disinfection units, powered by solar panels, provide chemical-free bacterial control, extending the life of filtration systems while ensuring water safety.
Water recycling in oil operations
The industry has flipped the script on produced water—the water that comes up with oil during extraction. Once considered waste, it’s now a valuable resource.
Advanced ceramic membranes separate oil from water at higher temperatures than traditional systems, enabling direct recycling without cooling steps. This saves both energy and processing time.
Supercritical water oxidation destroys organic contaminants completely, producing water clean enough for reinjection or steam generation. Qatar’s offshore operations reduced freshwater imports by 60% using this approach.
Bio-based flocculants made from date palm waste—abundant in the region—replace chemical treatments in the initial separation stage, creating a circular economy approach to water management.
Mobile recycling units move between well sites, processing water on-demand and eliminating transportation costs and associated carbon emissions.
Innovative approaches to reduce freshwater consumption
The drive to minimize freshwater use has sparked incredible innovation. Waterless fracturing using CO2 or foam reduces water needs by up to 90% while improving production rates in tight formations.
Air cooling systems replace water-intensive cooling towers, saving millions of gallons annually. These hybrid systems use water only during peak summer conditions, reducing annual consumption by 75%.
Condensation harvesting technology captures atmospheric moisture even in arid conditions. Solar-powered units installed at remote facilities in Oman generate up to 200 liters of water daily from thin air.
Smart irrigation systems using treated wastewater maintain necessary vegetation around facilities with 40% less water through soil moisture monitoring and weather-adaptive scheduling.
Digital twin modeling optimizes water use across entire operations, identifying interconnection opportunities between systems that weren’t apparent before. One major operator reduced overall water intensity by 28% through facility-wide implementation of these models.
Natural Gas Extraction Advancements
Techniques for handling high-sulfur gas reserves
The Middle East sits on some of the world’s gassiest gas reserves. But here’s the catch – much of it comes loaded with sulfur that’ll corrode equipment faster than a sandstorm strips paint.
Today’s sweetening technologies have revolutionized how we handle this sour gas. Membrane separation systems now remove hydrogen sulfide with 30% less energy than traditional amine treatments. At Qatar’s North Field, they’ve implemented dual-stage Claus units that recover 99.2% of sulfur – turning a problematic impurity into a valuable export commodity.
Smart materials are changing the game too. New ceramic catalysts in sulfur recovery units withstand temperatures up to 1,600°C while maintaining structural integrity for over 5 years – double the lifespan of previous materials.
LNG processing innovations
The LNG boom across the Middle East didn’t happen by accident. It’s all about the tech.
Mixed refrigerant processes have transformed cooling efficiency. The AP-X process deployed in Qatar liquefies natural gas using 8% less energy than conventional cascade systems, allowing production of 7.8 million tonnes per annum on a single train.
Modular construction has slashed installation times by 40%. In Oman, pre-fabricated modules for their LNG facility arrived 85% complete, cutting on-site work dramatically.
Floating LNG (FLNG) facilities are the latest breakthrough. Saudi Aramco’s upcoming FLNG vessel will process 3 million tonnes yearly while requiring just 25% of the footprint of traditional land-based facilities.
Associated gas capture and utilization
Remember when gas flaring lit up the desert night? Those days are ending.
Portable compression units now capture associated gas right at the wellhead. In Abu Dhabi’s fields, these systems redirect 95% of what used to be flared gas directly into collection networks.
Micro-GTL (Gas-to-Liquids) technology converts smaller volumes of associated gas into synthetic crude that can be blended with produced oil. Kuwait Oil Company’s pilot units process 5-10 million standard cubic feet daily, turning a waste product into valuable liquid hydrocarbons.
The UAE has pioneered using associated gas for carbon capture projects. Their Al Reyadah facility captures 800,000 tons of CO₂ annually from gas processing, injecting it into oil fields to enhance recovery while reducing emissions – a perfect example of circular thinking in modern extraction.
Digital Transformation in Well Operations
AI and Machine Learning for Predictive Maintenance
The Middle East oil industry is rapidly adopting AI-powered predictive maintenance systems that completely transform how well failures are handled. Gone are the days when equipment had to fail before being fixed. Today’s smart systems can spot potential issues weeks before they cause problems.
Companies like Saudi Aramco are using machine learning algorithms that analyze thousands of sensor data points to detect subtle changes in equipment performance. These systems can predict pump failures, identify corrosion risks, and even detect minor leaks long before they become catastrophic.
The results? Maintenance costs down by 30%. Unplanned downtime reduced by 45%. That’s millions saved across operations.
Cloud-Based Monitoring and Control Systems
Real-time well monitoring has taken a giant leap forward with cloud systems that give operators unprecedented control from anywhere in the world.
The UAE’s ADNOC implemented cloud monitoring across 650 wells, allowing teams to make instant decisions based on live data streams. These systems connect previously isolated operations into a single, accessible platform.
What makes cloud systems different?
- Remote access from any device
- Instant alerts when parameters drift outside optimal ranges
- Historical performance tracking with one click
- Secure data sharing between field teams and headquarters
Digital Twin Technology for Well Lifecycle Management
Digital twins might sound like science fiction, but they’re revolutionizing how Middle Eastern operators manage wells from planning to abandonment.
Qatar Petroleum created exact virtual replicas of their offshore wells, allowing engineers to test scenarios without risking actual equipment. These virtual models simulate every aspect of well performance under countless conditions.
Engineers can virtually:
- Test different production scenarios
- Simulate interventions before performing them
- Train staff on emergency procedures
- Predict long-term well behavior
Big Data Analytics for Performance Optimization
The sheer volume of data generated by a single well is staggering. Modern operations in Kuwait’s oil fields generate terabytes of information daily – pressure readings, temperature data, flow rates, chemical compositions.
Big data platforms now crunch these numbers in real time, revealing optimization opportunities that were invisible before. One Kuwaiti operation increased production by 15% simply by adjusting parameters based on data insights.
The most successful operators use analytics to balance production rates against long-term reservoir health, ensuring maximum recovery without damaging future production potential.
Environmental and Sustainability Innovations
A. Methane detection and reduction technologies
The Middle East oil industry has woken up to the methane problem in a big way. Companies are deploying advanced optical gas imaging cameras that can literally see methane leaks invisible to the naked eye. These handheld devices let technicians spot and fix leaks on the spot.
Drone technology has changed the game completely. Equipped with specialized sensors, these drones fly over vast oil fields and processing facilities, identifying methane hotspots in minutes instead of days. Some operators in Qatar and the UAE have cut methane emissions by 45% just by implementing regular drone surveillance programs.
Smart continuous monitoring systems are becoming standard at well sites. These sensors provide real-time data on methane levels, triggering automatic alerts when leaks occur. The newest systems even use machine learning to predict potential leaks before they happen.
B. Zero-flaring initiatives and equipment
Gas flaring used to be just part of the landscape in Middle Eastern oil fields. Not anymore. Companies have invested billions in gas capture systems that redirect previously flared gas into productive use.
Mobile gas processing units now follow drilling operations, capturing associated gas that would have been flared. These compact units compress and process the gas right at the wellsite.
Saudi Aramco’s MERAD system (Methane Emission Reduction At Drilling) has eliminated routine flaring at over 200 well sites since 2019. The technology recycles gas back into the process stream instead of burning it off.
High-efficiency enclosed combustors have replaced traditional flare stacks at many sites, reducing emissions by up to 99.9% when flaring can’t be avoided entirely.
C. Carbon capture and storage implementations
The Middle East leads in large-scale carbon capture. The Al Reyadah facility in Abu Dhabi captures 800,000 tons of CO2 annually from Emirates Steel, injecting it into aging oil fields for enhanced oil recovery.
Saudi Arabia’s Uthmaniyah project captures over 500,000 tons of CO2 yearly from gas processing operations, demonstrating the region’s commitment to carbon management.
Novel carbon mineralization technologies are being tested in Oman, where CO2 is converted into stable carbonate minerals by reacting with the country’s abundant peridotite rock formations.
D. Reduced footprint drilling and production methods
Multi-well pad drilling has revolutionized the industry’s physical footprint. A single pad can now access over 30 wells through directional drilling, reducing surface disturbance by up to 90%.
Extended reach drilling techniques pioneered in Qatar allow operators to reach reservoirs up to 12km away from a single surface location, minimizing environmental impact in sensitive areas.
Waterless fracturing using CO2 or nitrogen foam has gained traction in water-scarce Middle Eastern regions, conserving precious water resources while maintaining production efficiency.
E. Solar-powered well operations
The irony isn’t lost on anyone – using the abundant Middle Eastern sunshine to power oil extraction. Solar-powered pump jacks are becoming a common sight across the region, with over 2,000 units deployed in Oman alone.
Solar desalination systems now provide water for injection and operational needs at remote well sites, reducing both emissions and water transportation costs.
Battery storage systems paired with solar installations ensure 24/7 operations, eliminating the need for diesel generators even during nighttime operations.
Kuwait Oil Company’s solar-powered artificial lift systems have reduced operational carbon emissions by 22,000 tons annually while cutting operating costs by $18 million.
The Middle East’s oil industry continues to evolve through remarkable technological innovation. From advanced drilling systems and smart well engineering to sophisticated water management in harsh desert environments, the region has embraced cutting-edge solutions to maximize efficiency and production. Digital transformation has revolutionized operations through AI, IoT, and real-time monitoring, while environmental sustainability has become increasingly central to industry practices.
As technology continues to advance, Middle Eastern oil-producing nations are well-positioned to maintain their global leadership in energy production. Companies and professionals in this sector should stay informed about emerging technologies and sustainable practices to remain competitive. The future of well operations in the region will be defined by those who can successfully balance technological innovation with environmental responsibility, ensuring the industry’s continued prosperity while addressing the challenges of a changing world.